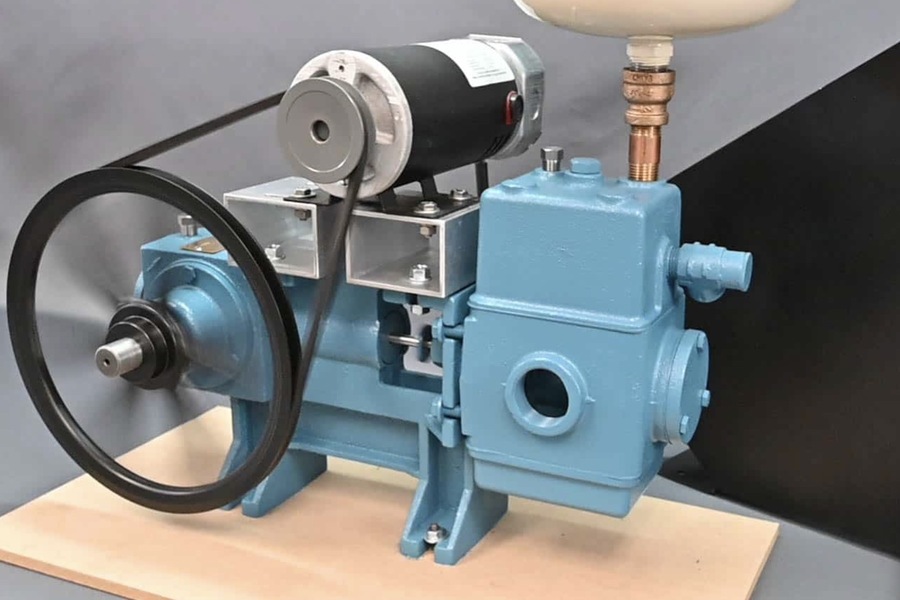
Piston Pumps: Operating Principle, Classification, Advantages, and Maintenance
Piston pumps are a robust category of positive displacement pumps recognized for their high reliability, strong suction capability, and ability to create significant discharge pressures. These pumps are widely used in industries ranging from fuel and oil transfer to hydraulic systems and chemical processes. They offer versatility, allowing them to handle various liquids and applications, from circulation and cargo transfer to hydraulic steering on modern tankers. Companies like Ghaima Group of Companies play a key role in supporting these industries, providing expertise in maintenance and engineering solutions for these complex devices. This article provides an in-depth look at the operating principles, classification, advantages, disadvantages, and maintenance practices associated with piston pumps, highlighting their importance across diverse industries.
Operating Principle of Piston Pumps
The operating principle of a piston pump relies on a reciprocating piston mechanism within a cylinder. This reciprocation process involves two main strokes—suction and discharge:
- Suction Stroke
As the piston retracts, it creates a vacuum in the cylinder, opening the suction valve. This pressure difference causes the liquid from an external source to enter the cylinder. - Discharge Stroke
As the piston moves in the opposite direction, it compresses the liquid, creating pressure within the cylinder. This pressure closes the suction valve and opens the discharge valve, allowing the liquid to exit through the discharge line.
This alternating action results in a continuous pumping cycle, moving fluid with high pressure and consistency. Rotary piston pumps, a variant of the traditional piston pump, are particularly useful in hydraulic systems, where they provide smooth control over the direction and speed of steering at a constant operational speed.
Classification of Piston Pumps
Piston pumps can be classified in multiple ways based on factors like flow rate, drive type, connection, shaft speed, piston design, cylinder arrangement, pumped liquid type, and mode of action. Each classification reflects the pump’s suitability for specific applications and operational environments.
1. Classification by Flow Rate
The flow rate classification is based on the volume of liquid the pump can handle, typically measured in cubic meters per hour (m³/h).
Low-flow pumps: Up to 20 m³/h.
Medium-flow pumps: 20 – 60 m³/h.
High-flow pumps: Over 60 m³/h.
2. Classification by Drive Type
The drive type classification denotes the type of power source used to operate the pump:
Manual: Operated manually; ideal for low-flow or emergency applications.
Electric: Driven by an electric motor; common in industrial settings due to ease of automation.
Steam: Powered by steam; typically used in older industrial environments or where steam power is available.
Mounted: Driven by a specific power source, such as a hydraulic or pneumatic system, for specialized applications.
3. Classification by Engine Drive Connection
This classification determines how the pump is connected to its engine drive:
Driven: These pumps are linked to a crankshaft or other mechanism, often using a crank journal and eccentricity, allowing for controlled, rhythmic pumping action.
Direct Acting: Connected directly to the engine drive, providing a straightforward and efficient power transfer.
4. Classification by Drive Shaft Speed
Drive shaft speed influences the pump’s flow rate and pressure:
Low-speed: Operate at speeds up to 80 RPM.
Normal-speed: Function at speeds up to 150 RPM.
High-speed: Run at speeds up to 350 RPM.
Ultra-high-speed: Operate at speeds up to 750 RPM, used in high-pressure applications with limited space.
5. Classification by Piston Design
The design of the piston influences the flow and pressure characteristics:
Disk Pistons: Utilize a flat disk piston, providing efficient sealing and reliable performance.
Plunger Pistons: Feature a plunger-type piston, allowing higher pressures and improved sealing.
Ball Pistons: Equipped with a ball-shaped piston, commonly used in compact, high-precision applications.
6. Classification by Cylinder Axis Arrangement
The arrangement of the cylinder’s axis impacts the pump’s structure and orientation:
Horizontal: Offers stability and easy installation, commonly used in ground-mounted applications
Vertical: Suitable for space-constrained environments or vertical installations.
7. Classification by Type of Pumped Liquid
Piston pumps can handle a range of liquids, making them suitable for specialized applications:
Water: Used in general water pumping applications.
Oil: Suitable for oil transfer in industrial systems.
Brine: Designed for pumping saline solutions, often used in desalination.
Fuel: Suitable for fuel transfer in transportation and storage.
8. Classification by Mode of Action
The mode of action classification defines whether the pump operates in one or both directions:
Single-acting: Fluid is pumped in one direction with each piston stroke.
Double-acting: Fluid is pumped in both directions, providing continuous flow and increased efficiency.
Advantages and Disadvantages of Piston Pumps
Advantages
- High Pressure Capability: Piston pumps can achieve pressures up to 2-4 MPa, ideal for high-pressure applications.
- Dry Suction Ability: They can lift liquids without the need for pre-priming.
- High Volumetric Efficiency: These pumps have an efficiency rate of up to 0.99, reducing leakage and energy loss.
- Consistent Pressure Control: By adjusting the rotation speed, the flow rate can be regulated without altering the pump’s pressure output.
Disadvantages
- Uneven Flow Rate: The reciprocating motion can lead to flow irregularities, causing pulsations.
- Weight and Size: Piston pumps are generally large and heavy, making them less suitable for space-restricted environments.
- High Manufacturing and Repair Costs: The complex design and components result in relatively high production and repair costs.
- Sensitivity to Fluid Characteristics: Certain fluids may affect the pump’s performance or cause wear over time.
- Frequent Valve Maintenance: The suction and discharge valves are prone to wear and blockage, requiring regular maintenance.
Maintenance of Piston Pumps
Proper maintenance of piston pumps is critical due to their high-pressure capabilities and sensitive components. Specific maintenance protocols are essential to ensure reliable operation and prevent mechanical issues.
General Maintenance Guidelines
- Routine Inspection: Regularly inspect the pump’s mountings, seals, and gaskets to ensure everything is in satisfactory condition.
- Lubrication: Ensure all moving parts, such as the piston, crankshaft, and bearings, are well-lubricated to prevent friction-related wear.
- Valve Maintenance: Regularly check the suction and discharge valves for signs of wear or clogging and replace them as needed.
- Check Oil Quality: In pumps with oil systems, monitor the oil level and quality, as impurities can cause wear on internal surfaces.
- Pressure Relief Verification: Test relief valves periodically to prevent accidental pressure spikes that could rupture pipelines or damage pump components.
- Startup Precautions: Always begin operation with the discharge and suction valves open, as running the pump with a closed valve can cause severe damage.
- Flow Regulation: Avoid regulating flow by throttling the discharge valve; instead, use speed adjustments or bypass lines to manage the pump’s flow rate.
Specialized Maintenance for Industrial Settings
In high-stakes industrial environments, piston pumps may encounter specific operational challenges. For instance, in the petrochemical or chemical industry, ensure that seals, gaskets, and internal components are compatible with the pumped liquid, as aggressive chemicals may degrade standard materials.
Applications of Piston Pumps
The versatility and high-pressure capabilities of piston pumps have made them a staple across industries, with applications ranging from feed and circulation to handling aggressive liquids in challenging environments.
Feed and Circulation Pumps: Used in water treatment and industrial processes where consistent liquid movement is required.
Oil and Fuel Transfer: Piston pumps are well-suited for loading and unloading petroleum products on tankers and in storage facilities.
Hydraulic Steering Systems: In hydraulic systems, rotary piston pumps provide precise steering control, which is essential in ships and heavy machinery.
Chemical Industry: Piston pumps’ resistance to aggressive liquids makes them ideal for handling chemicals, even under high-pressure conditions.
Key Takeaways
Piston pumps are critical components in modern industry, thanks to their ability to operate reliably under high pressure and their adaptability to a variety of liquids. However, their complex design requires regular maintenance and careful handling to ensure consistent performance. In regions like the UAE, where specialized services are available, companies like the Ghaima Group of Companies provide professional maintenance and repair services, helping industries maximize the lifespan and efficiency of their piston pumps.
In summary, while piston pumps are associated with a higher upfront investment and operational sensitivity, their versatility and ability to handle challenging fluids and pressures make them invaluable in various industrial applications. Proper maintenance, routine inspections, and adherence to operational guidelines can significantly enhance their longevity and performance, making them a worthwhile investment across a broad range of industries.
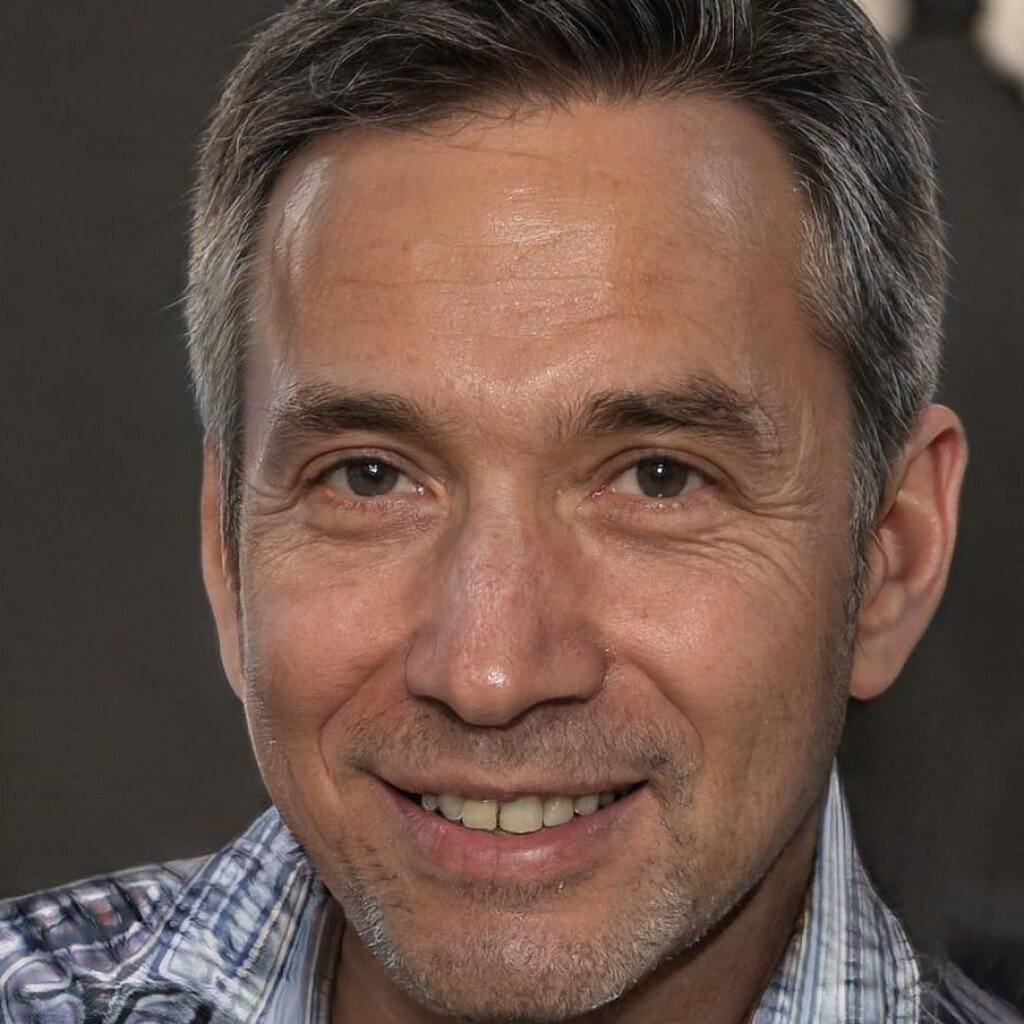
Fixie owner, coffee addict, audiophile, reclaimed wood collector and proud pixelpusher. Acting at the fulcrum of design and purpose to create strong, lasting and remarkable design. Nothing ventured, nothing gained.